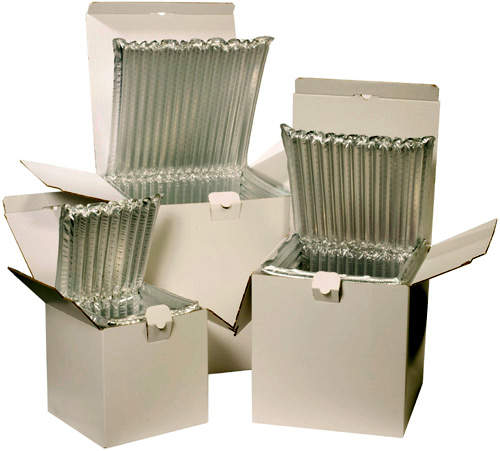
What do a bird in wintertime, a honeycomb and double glazing have in common? Instead of being some elaborate riddle, the answer is instead very simple. They are all ways to describe the cold chain storage technique on the market by Coldpack, which has recently had its UK launch.
Known as the Airliner, the packaging contains a honeycomb structure in its inflatable walls that acts like double glazing by mimicking the act of birds fluffing their wings in wintertime to keep warm.
The product offers a happy medium between the advantages of polystyrene and polyurethane and as such the Airliner product has carved out a niche market with pharmaceutical customers looking to ship small parcels.
The global nature of clinical trials and the shipping of drugs manufactured in one country for use in another have provoked this need for novel packaging techniques. With a global emphasis of cutting costs still in force around the world, making sure a product reaches a destination on time and intact has become paramount.
With Arena International’s co-located Cold Chain Storage & Distribution and Clinical Trial Supply conferences being held on 23 February in London and POUT New Jersey in March, the issue of cold chain storage in every part of the supply chain is becoming particularly prevalent.
Like bees to honey
How well do you really know your competitors?
Access the most comprehensive Company Profiles on the market, powered by GlobalData. Save hours of research. Gain competitive edge.
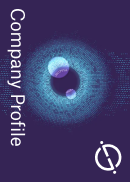
Thank you!
Your download email will arrive shortly
Not ready to buy yet? Download a free sample
We are confident about the unique quality of our Company Profiles. However, we want you to make the most beneficial decision for your business, so we offer a free sample that you can download by submitting the below form
By GlobalDataThe technology used in the Airliner is based on the notion of a thermal barrier created by a honeycomb structure. This comprises two layers of a DuPont Surlyn film, separated by the aluminium structure.
When filled with oxygen or argon, multiple compartments – known as baffles – are created to block calorie transfer and minimise heat, radiation, convection and conduction.
A grant given by the US Department of Energy to Berkeley University to develop a flexible storage technique that could regulate temperature in the 1990s saw the technology being first developed in the US. However, the sale of the innovation’s licence and a company buy-out resulted in the product’s home being transferred to France.
Coldpack sales director Arnaud Adam says companies with 24 to 48 hour shipping requirements have drawn the most demand, largely because cost effectiveness is key. “The second typical case is customers who are looking for heavy duty installation because they are shipping for 72 to 96 hours,” he explains.
“At that stage the price of the packaging is not really the issue but more that the cargo is so precious it has to arrive in perfect shape.”
Like all packaging that serves the global food and pharmaceutical industries, the temperature requirements on the Airliner are demanding. It has to be able to maintain a constant temperature level with products shipped from Europe’s winter where temperatures regularly plummet to -18°C, to Asia’s summer where they regularly hit the high 30°Cs.
This isn’t the only challenge that the cold chain industry faces. There is also constant emphasis on cutting the size of packaging to save space while providing a cushion to minimise breakages. Coldpack’s recently opened manufacturing facility in Münster, Germany, which after four years in the making now produces a new generation of films on reels that can be converted into a variety of shapes, targets this market.
Its initial spin-off, the one-day pharmaceutical pouch, is its first offering. It takes the shape of an inflatable thermal envelope that is capable of keeping products between +2°C and +8°C.
“Critically, we have designed a pouch that allows the pharma industry to mix temperature-sensitive and non-temperature-sensitive medicines in the same crate,” Adam says.
Eco-awareness
In 2009 a number of directives and action plans were put in place around the world to minimise the quantity of packaging waste. Although waste from pharmaceutical packaging may not be hazardous like other substances thrown away from drug manufacturers, the drive to make it as “green” as possible is a trend sweeping the industry.
For this reason, polystyrene is avoided by the most environmentally conscious distributors. Although the Airliner product can not be re-inflated once it has reached the end of its life, it is flexible and easily deflated to a small size, so it still offers advantages over polystyrene.
An assessment by independent consultants on a 30-year lifespan of the product found that compared to polystyrene, the Airliner used 40% less oil in its manufacturing processes.
Thinking outside the box is sometimes just what is needed to protect what is inside the package. A host of technologies are on their way to revolutionising the pharmaceutical and food packaging arena – not least the developments in radio-frequency identification technology to allow the tracking of packages around the world. With industry experts set to meet to push ideas forward in the coming weeks, it is certainly an area to watch.