For those involved in the clinical supply chain, if you ask around to find out how they feel processes can be improved, you’ll receive a plethora of responses. Chief among them, the ability to ensure a package is moved along expeditiously without hitch is top of the list. However, ask them what their biggest challenges are, invariably, you get the same answer.
Sustaining the temperature of a product and the lack of visibility of shipments are the most pressing concerns. With sponsors shipping a lot of cold chain products around the world, the challenge is to maintain the integrity of that temperature and the time for delivery. And the reason for that is simple. Experts say if anything goes wrong with the shipment, the delay could set a clinical trial back months, if not years. With that said, it’s vital companies know what condition their products are in.
"On a global scale, my biggest problem is maintaining temperatures during transit and customs clearances, particularly for refrigerated products," said Rich Nelson, Distribution Services Manager, PCI Services.
Nelson handles the PCI’s international activities on a daily basis. He said that, compared to frozen products, maintaining the temperature for a refrigerated product (within the 2-8°F range) poses greater challenges. This is because "there are so many different shippers that if I’m not using the same shipper that the courier can replenish then I have all sorts of issues."
The debate on how to mitigate this dilemma has raged on for many years. The general consensus within industry appears to come down to effective communication between the sponsor and the carrier throughout every step of the journey. With technology continuing to advance, there are technological solutions, too. Monitoring devices placed on the product itself can be used to observe its temperature. Further, GPS trackers or a form of satellite device can send companies information in real time.
See Also:
Brad Elrod, Director, Global Conveyance, Pfizer, says his company has done this before, especially during later stage trials when the stakes are higher and time is precious. "If we’re shipping a large batch of materials, we put the tracker into the shipping container with the product in it," Elrod said, "so when it’s sending a signal out you can monitor where it is and when it gets there."
How well do you really know your competitors?
Access the most comprehensive Company Profiles on the market, powered by GlobalData. Save hours of research. Gain competitive edge.
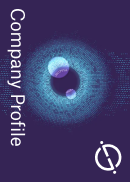
Thank you!
Your download email will arrive shortly
Not ready to buy yet? Download a free sample
We are confident about the unique quality of our Company Profiles. However, we want you to make the most beneficial decision for your business, so we offer a free sample that you can download by submitting the below form
By GlobalDataWith the cost of developing drugs on the rise, the idea of adding GPS trackers to each shipment would incur an extra cost to what is already an expensive process. Wouldn’t that add an extra burden? Naturally there are pros and cons. Elrod said the cost wouldn’t be obstructive or overbearing. Ultimately, he says it boils down to weighing up how critical it is to know where the shipment is and condition it’s in.
One supply chain professional who’s in agreement with Elrod is Bob Albanese, Senior Vice President of Strategic Development at CSM (Clinical Supplies Management).
"For the accuracy of our delivered shipments, we use multiple tools – validated shippers, preferred couriers, active and passive temperature monitoring, location monitoring," he said.
Albanese says for all the issues surrounding shipping clinical supplies, sponsors need to address the root cause of the problem. This, he says, occurs before the trial begins when a sponsor is developing the design of the study and can’t foreshadow potential problems that will occur in the supply chain. Certainly, it can be argued the industry has been using an outdated model, which requires enough supplies to be on siteand available to multiple patients, regardless of enrolment rates. This can become risky when it comes to drug conservation.
"We work directly with our clients to better design their studies using a customized supply chain model that ensures optimum drug conservation," Albanese said. "We’re investigating medicines sometimes for the first time use ever; there’s not a clear path or model to follow. Every study is different and presents different challenges."
With that said, companies need to strategically plan for change at every juncture throughout the supply chain. The old model, according to Albanese, assumes nothing will change and, in that regard, the industry needs to adjust its mindset.
"Having a change strategy in place that accounts for every variable is crucial," he said.
To guard against these problems, companies must co-ordinate with couriers ahead of the shipment. The key is preparation. Further, the more you can do upfront before clinical supplies are shipped, the less likely you’ll encounter problems when the shipment gets to the other end.