Many Korean pharmaceutical companies have internal facilities to manufacture their drugs. However these facilities for manufacture cater to the full pipeline of drug development. From a business perspective, commercial drugs are produced on a larger scale and have significant value to the company, and as a result are often prioritized on the production line within the manufacturing facility. Clinical drugs (IPs) are generally produced in much smaller amounts, and despite the consequence of prolonged manufacturing time to clinical teams, the importance of speedy IP manufacture is not always appreciated on the manufacturing line.
Of course manufacturing facilities are working to tight and complex timelines, and commercial drug production takes up the bulk volume in this case. It therefore can be difficult for a clinical manager to persuade facilities to agree and meet timelines for clinical products.
From a clinical perspective, a delay in manufacture can pose a risk to the trial in various ways; a delay to the trial could pose risks to patient retention, site activation timelines and ultimately, trial protocol. The cost of a delay to trial is significant to a drug development company; however it can be outweighed by the loss of revenue, from delayed commercial drug production.
An added complexity to this point centers around the notice given to manufacturing plants across the two product types. Commercial production tends to have more time for planning due to the large and complex nature of their distribution. IP manufacture may be required at short notice, to adapt to changing results in patient recruitment or as a consequence of trial results. This makes it especially difficult for the trial planning team to gain priority of their IP manufacture if they require interruption of commercial manufacture.
So what is the solution? For larger companies who can develop a more robust structure, a dedicated trial supply team can work together with manufacturing teams to streamline communications, expectations, plans and consequences. However for smaller companies this remains a conundrum, and presents the question about whether outsourced manufacture could better support clinical supply teams.
Logistics: Preventing Slow Down and Quality Loss from Providers
A key requirement for any drug development company, especially for high value product development, is to ensure drug is stored at GSP qualified depots. Qualified depots can be hard to come by in Korea. For products with tight temperature parameters it is crucial that the quality of the storage is high and for a manufacturer, the GSP qualification assures that. Typically trial sponsors have to use external storage facilities, which cause an added concern due to the mix of products stored for competitive companies on site.
How well do you really know your competitors?
Access the most comprehensive Company Profiles on the market, powered by GlobalData. Save hours of research. Gain competitive edge.
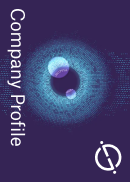
Thank you!
Your download email will arrive shortly
Not ready to buy yet? Download a free sample
We are confident about the unique quality of our Company Profiles. However, we want you to make the most beneficial decision for your business, so we offer a free sample that you can download by submitting the below form
By GlobalDataFrom a logistics perspective, drug shipments and logistics are largely handled by specific providers of these services. Locally there can be challenges with retention of staff within these groups, and this presents problems to the trial sponsor who is often working with partners without the necessary knowledge of clinical products and importantly, requirements for the transport of temperature maintained products. Having said this, often even long term staff can lack an in depth knowledge of clinical logistics. Potentially, the answer could be development of robust and specific SOPs internally. A trial sponsor cannot impact this issue; however there is a general concern which can be abated with tighter internal processes from service providers locally.
Where logistics can be especially challenging is upon supplying to new markets regionally. Each region has its own complexities, especially regarding regulations. Although most companies have access to a degree of regulatory information about entering a new region, there are details which can only be learned from experience which are unknown in the first instance. Logistics providers could offer real support here. For service providers regularly working in these regions there is a host of information they could offer to support trial sponsors. What would be unparalleled in value would be a database which lists key information, regulatory and other to learn before shipping to a new market.
Temperature Maintenance: Minimizing Cost of Temperature and Tracking Technology
Aside from storage, the biggest issue for temperature maintained products is in the instance of temperature excursion during the shipment. Any recording of excursion from the range of qualified temperatures requires full return of shipment to the trial sponsor. The cost of returning a shipment in this instance is enormous, but necessary. It is an incentive to better control the temperature of the shipment through technology investment, education of supplier and supplier choice, however when it does happen, the costs are not accounted for. The industry needs to find a more efficient way to return shipments in order to lower the cost in these instances, but the answer to this is not clear.
What could act as a preventative measure perhaps, and certainly as an opportunity to improve efficiency, is an automated method of tracking shipment of the IP, as well as blood samples or devices, similar to that which is already available for other shipped packages. At the moment, regular communication with the logistics provider is required to receive updated information on shipments. What would be simpler would be to log in to the provider homepage, and see simple accounts of the shipment movement.
For example, a simple graph or diagram would indicate any potential changes, and communication with the provider can be sought when necessary, minimizing the time spent checking in on product shipments. This process would also ensure that products aren’t delayed in customs on arrival. If the trial sponsor can easily access real-time tracking on a daily basis, any concerns with customs will be picked up by the trial sponsor immediately and either handled, or in the worst case, the trial sponsor can initiate new manufacture and speed up the replacement shipment preventing delay to the trial.